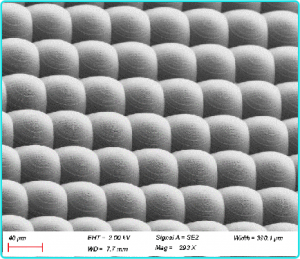
微纳加工 | 光电器件常用基板/衬底
硅
在集成电路中,硅是作为标准材料使用的,也是世界上研究最广泛的一种材料。这种材料适用作高温半导体,是一种容易生长的氧化物绝缘材料。这些特性及目前所有的工业基础设施和模具,使集成硅光学器件的研发倍受关注。硅材料应用于诸如发光二极管(LED)、波导和太阳能电池等光电器件,以及微机电系统(MEMS)中。
传统的各向异性湿法刻蚀化学加工硅的方法是使用KOH∶H2O(按重量1∶1)刻蚀剂,在80℃温度下,刻蚀速率约为1.4μm/min。在硅的微加工工艺中常采用这种化学法加工通孔或分离薄膜。用SF6化学刻蚀剂完成硅材料的各向异性干刻蚀。通过对极高长宽比干刻蚀工艺的后续研究获得了深反应离子刻蚀(DeepReactiveIonEtch,DRIE)技术。该技术交替使用SF6/Ar和CHF3/Ar化学刻蚀剂。这种混合气体能够促使一种类特氟隆的聚合物淀积在曝光过的所有表面上。由于离子轰击,SF6/Ar工序会快速消除水平表面上的聚合物,并对曝光过的硅表面进行刻蚀。该共聚物处理工序可以避免刻蚀到侧壁,能够形成高各向异性的轮廓分布。
使用电子束光刻术可以在硅基板上加工出小于10nm的PMMA线宽。美国桑迪亚国家实验室已经加工出许多硅材料光学器件,包括表面微机械反射镜器件和聚光太阳电池。
砷化镓
砷化镓(GaAs)是一种应用在各种电子器件和光电器件中的标准半导体材料。由于砷化镓的内禀性,一般地,高工作频率、电子迁移率和光发射特性都优于硅材料的同类性能。已经根据这些特性制造出各种光电器件,如太阳电池、探测器和量子阱激光器。砷化镓在2~5μm整个波段都是透明的,并有高折射率。与硅材料相比,砷化镓的缺点是缺少一个活泼的本征氧化物。由于高速和大功率应用领域砷化镓器件加工技术的快速发展,该材料的处理工艺细节为大家所了解。
一般来说,砷化镓材料中电荷传输是足够的,不需要耗电层,所以非常适合使用电子束光刻术。已经证明,在PMMA上得到的单个抗蚀剂沟槽线宽小于20nm。
使用几种氧化剂,包括过氧化氢(H2O2)及诸如溴之类的卤族物质,就能够完成砷化镓材料的湿法刻蚀。如用一种H2PO4∶H2O2∶H2O(3∶1∶50)刻蚀液完成沿(111)面的各向异性刻蚀。建议选择的一种刻蚀剂比例是柠檬酸∶H2O2∶H2O为5g∶2mL∶5mL。例如,砷化镓和砷化镓铝(AlGaAs)间的选择性是(10~1000)∶1,并且,为外延层提供牺牲保护刻蚀。
其他研究者利用砷化镓铝刻蚀定影剂对砷化镓优化出一种可选择的各向异性刻蚀工艺。电感耦合等离子体(ICP)系统使用一种BCl3∶SF6∶N2∶He化学混合液,它对砷化镓比对砷化镓铝的选择性高200倍。该工艺对具有极高各向异性的砷化镓材料能够产生良好的侧壁钝化。
在美国桑迪亚国家实验室,已经研发出一种化学辅助离子束干法刻蚀(Chemi-callyAssistedIonBeamdryEtch,CAIBE)工艺,在砷化镓材料上实现高各向异性特征分布,并应用于波片器件中。此工艺使用氩离子激光束控制样品表面环境反应气体的实际量和流速。在这种情况中,环境反应气体是氯气(Cl2)和三氯化硼(BCl3)的混合气体。为使侧壁钝化和沟槽深度达到最大,要对刻蚀条件进行优化。
熔凝石英
熔凝石英是一种包含有非晶体二氧化硅(SiO2)的玻璃。由于高纯度的合成工艺,熔凝石英的光学和热性质都优于其他类型的玻璃。熔凝石英有非常低的热膨胀系数(在20~320℃温度范围内约5.5×10-7cm/(cm·K)),非常适合极端温度和/或温度变化的环境。该材料从紫外到中红外光谱区有很高的透过率和较低的折射率(并有低的菲涅尔反射损失),所以熔凝石英是一种理想的光学材料。这种材料能够应用于各种微流体器件及宽波段光学元件。
已经专门研发出适用于熔凝石英材料的各种技术,以便利用现代超净设备处理这种材料。前期的研究重点是,利用氢氟酸(HF)进行湿法刻蚀和微流体器件的晶片焊接。熔凝石英是一种非晶体材料,所以在进行湿法化学刻蚀期间会观察到各向同性轮廓分布。利用光刻术和氢氟酸缓冲液,可以在熔凝石英上制成近乎理想的半圆柱形。使用晶片焊接技术(温度约1000℃),能够制造出圆柱形微流体通道。
用近代纳米技术制造出的光学器件可具有梯度或者带角度的轮廓分布,从而实现菲涅尔透镜或其他衍射元件的功能,例如二元光学元件、梯度折射率透镜和亚波长人造梯度折射率透镜。美国桑迪亚国家实验室的研究人员利用几个循环的电子束光刻术和反应离子刻蚀技术(RIE)已经制造出具有多个台阶轮廓分布的熔凝石英二元透镜。研究人员组合使用一块镍(Ni)掩模板(含有铬(Cr)或钛(Ti)附着层)和一种最佳刻蚀剂配比———40sccm(标准流量)的三氯甲烷(CHF3)和3sccm氧气,并施加40mTorr压力和396V基座偏压具有200W射频功率,从而得到了极高各向异性的轮廓分布,
熔凝石英材料的质量对器件的最终质量有着重要影响。低质量的熔凝石英在反应离子刻蚀工艺后可能出现空洞或使表面粗糙,或者凹凸不平。因此,选择高质量基板以实现最佳各向异性和表面平滑度,这也几乎是对光学元件的最基本要求。
我们提供快速MEMS器件 / 微纳米结构加工设计服务, 欢迎留言咨询。