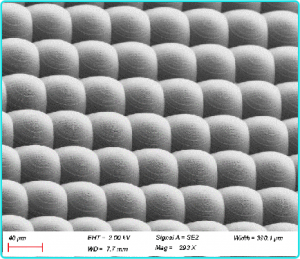
Micro and Nano Processing | Substrates / Substrates for Optical Devices
Silicon
Silicon is used as a standard material in integrated circuits and is one of the most widely studied materials in the world. This material is suitable for use as a high temperature semiconductor and is an easy to grow oxide insulating material. These properties and all the current industrial infrastructure and tooling have made the development of integrated silicon optical devices of great interest. Silicon materials are used in optoelectronic devices such as light-emitting diodes (LEDs), waveguides and solar cells, as well as in microelectromechanical systems (MEMS).
Traditional anisotropic wet etching of chemically processed silicon uses a KOH:H2O (1:1 by weight) etchant with an etching rate of about 1.4 μm/min at 80°C. This chemical method is often used in silicon microfabrication processes for through-hole processing or separation of thin films. Anisotropic dry etching of silicon materials is accomplished with SF6 chemical etchant. The DeepReactiveIonEtch (DRIE) technique was obtained through subsequent studies of the very high aspect ratio dry etching process. This technique uses alternating SF6/Ar and CHF3/Ar chemical etchants. This gas mixture promotes the deposition of a polymer of Teflon on all exposed surfaces. Due to ion bombardment, the SF6/Ar process quickly removes the polymer from the horizontal surface and etches the exposed silicon surface. This copolymer treatment process avoids etching into the sidewalls and allows for a highly anisotropic profile distribution.
PMMA line widths of less than 10 nm can be processed on silicon substrates using electron beam lithography. Sandia National Laboratories has processed many optical devices in silicon, including surface micromechanical reflector devices and concentrating solar cells.
Gallium Arsenide
Gallium arsenide (GaAs) is a standard semiconductor material used in a variety of electronic and optoelectronic devices. Due to the endowment of GaAs, the high operating frequency, electron mobility and photoemission properties are generally superior to those of its silicon counterpart. Various optoelectronic devices have been fabricated based on these properties, such as solar cells, detectors, and quantum well lasers. Gallium arsenide is transparent in the entire band from 2 to 5 μm and has a high refractive index. The disadvantage of GaAs compared to silicon materials is the lack of an active intrinsic oxide. Due to the rapid development of processing technology for GaAs devices for high speed and high power applications, the details of the processing of this material are known to everyone.
In general, the charge transport in GaAs materials is sufficient without a power dissipation layer, making it ideal for the use of electron beam lithography. It has been demonstrated that the line width of individual resist trenches obtained on PMMA is less than 20 nm.
Wet etching of GaAs materials can be accomplished using several oxidizers, including hydrogen peroxide (H2O2) and halogenated substances such as bromine. For example, an H2PO4:H2O2:H2O (3:1:50) etchant is used to complete anisotropic etching along the (111) surface. The recommended etchant ratio is 5g:2mL:5mL of citric acid:H2O2:H2O. for example, the selectivity between GaAs and AlGaAs is (10~1000):1, and sacrificial protection etching is provided for the epitaxial layer.
Other researchers have optimized a selective anisotropic etching process for gallium arsenide using an aluminum gallium arsenide etch fixer. The inductively coupled plasma (ICP) system uses a BCl3:SF6:N2:He chemical mixture that is 200 times more selective for GaAs than for AlGaAs. The process is capable of producing good sidewall passivation for GaAs materials with very high anisotropy.
A chemically assisted ion beam dry etching (Chemi-callyAssistedIonBeamdryEtch, CAIBE) process has been developed at Sandia National Laboratories, USA, to achieve highly anisotropic feature distribution on GaAs materials for application in wave-sheet devices. This process uses an argon ion laser beam to control the actual amount and flow rate of the ambient reactive gas on the sample surface. In this case, the ambient reactive gas is a mixture of chlorine (Cl2) and boron trichloride (BCl3). To achieve maximum sidewall passivation and trench depth, the etching conditions are optimized.
Fused Silica
Fused silica is a glass that contains amorphous silicon dioxide (SiO2). Due to the high purity synthesis process, the optical and thermal properties of fused silica are superior to those of other types of glass. Fused silica has a very low coefficient of thermal expansion (approximately 5.5 x 10-7 cm/(cm-K) over the temperature range of 20 to 320°C) and is well suited for environments with extreme temperatures and/or temperature variations. The material has a high transmittance and low refractive index (with low Fresnel reflection loss) from the UV to mid-IR spectral region, making fused silica an ideal optical material. This material can be used in a variety of microfluidic devices and wide-band optical components.
Various techniques applicable to fused silica materials have been developed specifically to handle this material using modern ultra-clean equipment. Previous research has focused on the use of hydrofluoric acid (HF) for wet etching and wafer soldering of microfluidic devices. Fused silica is a non-crystalline material, so an isotropic profile distribution is observed during wet chemical etching. Using photolithography and a hydrofluoric acid buffer, near-ideal semi-cylindrical shapes can be made on fused silica. Using a wafer soldering technique (temperature ~1000°C), cylindrical microfluidic channels can be fabricated.
Optical devices fabricated with recent nanotechnology can have gradient or angled profile distributions to perform the functions of Fresnel lenses or other diffractive elements, such as binary optics, gradient refractive index lenses, and subwavelength artificial gradient refractive index lenses. Researchers at Sandia National Laboratories have fabricated fused silica binary lenses with multiple step profile distributions using several cycles of electron beam lithography and reactive ion etching (RIE). The researchers used a combination of a nickel (Ni) mask (containing a chromium (Cr) or titanium (Ti) attachment layer) and an optimal etchant ratio - 40 sccm (standard flow) of trichloromethane (CHF3) and 3 sccm of oxygen - and applied 40 mTorr pressure and 396V base bias voltage with 200W RF power, resulting in an extremely high anisotropic profile distribution that
The quality of the fused silica material has a significant impact on the final quality of the device. Low quality fused silica may develop voids or make the surface rough, or bumpy, after the reactive ion etching process. Therefore, the selection of high quality substrates for optimal anisotropy and surface smoothness is almost the most essential requirement for optical components.
We offer fastMEMS device / micro and nanostructure processing design services, Feel free to leave a message to inquire.
Related Products
Related Reading
UV-LIGA Electroforming | Preparation of fine metal mesh panels with large thickness and high porosity
UV-LIGA Electroforming | Fabrication of Metal Array Stencils Current Preparation
Introduction to Physical Vapor Deposition (PVD) types, characteristics and applications
Introduction to Physical Vapor Deposition (PVD) Types, Characteristics and Applications Contents
Micro and Nano Processing | Electron Beam Lithography Processing Principle
Micro and Nano Processing | Electron Beam Lithography Principles and Available Optical Technologies