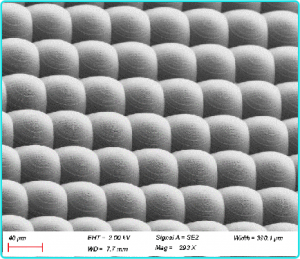
Micro and Nano Processing | Lithography - Electron Beam Lithography
Of all the non-optical lithography methods, this is the most commonly used. It uses an electron beam rather than photons to expose the resist to induce chemical changes, which subsequently leads to changes in solubility. However, unlike photolithography, it does not have a mask and the beam does not illuminate the entire substrate
The electron beam is generated, accelerated and focused to a small point and scanned over the substrate to create the image. The scanning mechanism is accomplished by a combination of mechanical translation of the substrate table as a tilt of the electron beam. The pattern is generated by modulating the beam current to turn on and off as the beam is scanned. The device is similar to a scanning electron microscope where the electron beam, steering coil and substrate are mounted in a high vacuum chamber.
The numerical aperture of electron beam systems is typically very low, on the order of 0.01. This has the benefit of a very large depth of focus. Despite the low numerical aperture, the expected resolution should still be in the order of 1 nm. However, in practice, this is not the case. The k1 parameter in the electron beam system is much larger than in the optical system. As we have seen before, the theoretical minimum possible value of k1 is 0.25, which for 10 keV electrons would lead to sub-nanometer resolution. However, in the current EBL system, the value of k1 is about 5. This is due to blurring caused by poor spherical and chromatic aberrations in the magnetic focusing system and the interaction of the electron beam with the substrate emitting secondary electrons. Therefore, the actual resolution of EBL is only in the range of 5 nm.
The biggest advantage of EBL is its high resolution. Due to the small numerical aperture, the depth of focus is also large. This makes it a very tolerant system for lithography on substrates with topographic features and small curvature. Currently, EBL is used extensively for manufacturing lithographic masks, especially when the required resolution on the mask is beyond what can be achieved by the laser scanner. This is by far the largest commercial application of EBL. In R&D, EBL is used whenever the desired feature is smaller than approximately 500 nm, by bypassing the mask and writing the pattern directly on the resist layer. Although immersion deep-UV projection can easily reach below 100 nm, such tools are typically not available outside of large production environments. Therefore, for research and development, EBL has become the first tool of choice for contact lithography stops. the biggest drawback of EBL is its slow speed. Because it is a scanning system, it is inherently slow. This speed is inversely proportional to the resolution, and it decreases as the beam spot size decreases to achieve higher resolution. Depending on the density of the pattern and the dose required, it can take several hours to write a 1×1-inch area. Another drawback is the requirement that the substrate be electrically conductive. As with scanning electron microscopy, the electron beam current needs to be grounded through the substrate to maintain charge neutrality. Any localized charging effects can significantly reduce resolution. For photomask writing, although the substrate is glass, a metal film is first deposited before the resist film is applied and that metal film is electrically grounded. Because silicon is partially conductive, writing on a resist film on a silicon substrate is also possible. Other cases of purely insulating systems will require careful consideration of how to dissipate the charge build-up.
We offer fastMEMS device / micro and nanostructure processing design services, Feel free to leave a message to inquire.