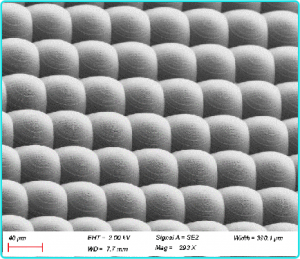
Micro-Nano Processing | Introduction to Electroplating Process
Electroplating is the process of depositing a metal or alloy on the surface of a substrate using the principle of electrolysis to form a uniform, dense, and well-bonded metal layer. Compared to thin film deposition techniques such as CVD and PVD, electroplating can use the principle of electrolytic deposition of metals to precisely replicate certain complex or specially shaped devices, and can increase the thickness of metals indefinitely.
1. Uses, advantages and disadvantages of common plating metals
Metal | Common Uses | Advantages | Not enough |
---|---|---|---|
Copper | Printed circuit boards, anti-carburization, increased conductivity, friction reduction during extrusion, repair of part dimensions, preparation of copper bumps, TSV, priming, conductivity | Good electrical conductivity, low stress, improved adhesion of plating layer and corrosion resistance | Copper is easy to oxidize, post-treatment needs to be done to prevent oxidation |
Nickel | Electrode materials, decorative and protective plating, and<br><br>priming,<br><br>MEMS structure. | Good plasticity, easy to extend the pressure, has good mechanical processing and mechanical properties, good stability, anti-oxidation, corrosion resistance, electroplated nickel deformation is small, low roughness, wear-resistant | May be magnetic<br><br>Nickel is easy to passivation, need to try to complete the plating at once, the intermediate power failure is prone to plating layer delamination. |
Gold | Applications in the electronics industry, aerospace, aviation, microelectronics and decorative technology, electrical conductivity, wire bonding | Excellent chemical stability. Soft gold is soft, very good ductility, strong bonding; hard gold has good wear resistance and is aesthetically pleasing. Used to improve conductive contact impedance and enhance signal transmission. | High gold cost. |
Silver | Electrode material, conductive | Good chemical stability, good aesthetics, improved conductive contact impedance, improved signal transmission | Light sensitive, easily oxidized |
Iron-Nickel | Soft magnetic materials | Strong magnetic properties, its corrosion resistance is comparable to that of nickel plating, its hardness is higher than that of nickel plating, and its toughness is better than that of bright nickel plating | |
Chromium Nickel | Resistors, thermocouples, gears, decorative plating | High hardness, heat resistance, with wear resistance, corrosion resistance, high resistance, oxidation resistance, good stability | Difficult to thicken the plating |
Tin | Application to the preparation of solderable plating materials | Good solderability | |
Platinum | Decoration, semiconductor package parts, electrodes | Soft texture, good ductility, good chemical stability | Plating temperature up to 92°C |
Palladium | Decorative, semiconductor packages | Chemically stable, good corrosion resistance, high plating hardness, very low and unchanging contact resistance | Requires high concentration of main salt in the plating solution |
2. Factors affecting the quality of plating
There are many factors affecting the quality of electroplated films, including current density, electric field distribution, line width, plating solution composition, and circulation method.
Tip effect: At the edge and tip of the workpiece or pole plate, more power lines tend to gather, a phenomenon called tip effect or edge effect. In plating, the tip effect can thicken, grow burrs or scorch the edges of the plating.
Current density: In electroplating production, the current passing through the workpiece surface per unit area is often called current density, which is usually measured in amperes per decimeter2 (A/dm2 or ASD). In general, low current density crystallization is delicate and soft, slow deposition speed and low productivity; high current density crystallization is coarse (burnt and powdered in serious cases) and hard, fast deposition speed and high productivity.
Impurities: All plating solutions contain impurities, usually from the chemicals used, impure anodes, additives, dissolution of substrates and photoresists during the plating process, etc. Organic impurities and metallic impurities can affect adhesion, produce pockmarks and pinholes, reduce dispersion and coverage ability, affect current efficiency and increase plating stress.
Extended Reading.
- Micro and Nano Processing | Overview
- Micro and Nano Processing | Photolithography - Nanoimprint Lithography
- Micro and Nano Processing | Lithography - Focus on Ion Beam FIB
- Micro and Nano Processing | Lithography - Electron Beam Lithography
- Micro and Nano Processing | Photolithography - Optical Lithography
- Micro and Nano Processing | Etching
- Micro- and Nanofabrication | Thin Film Preparation - Epitaxy
- Micro and Nano Processing | Thin Film Preparation - PVD
- Micro and Nano Processing | Thin Film Preparation - CVD