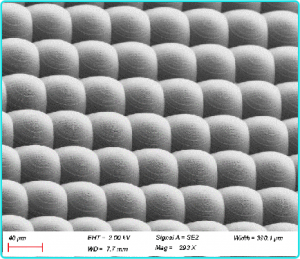
Micro and Nano Processing | MEMS Fine Processing
1.6 Sacrificial Layer Technology
Sacrificial layer technology is also called separation layer technology. In sacrificial layer technology, a micro part is formed on a silicon substrate by chemical vapor deposition, and a separating layer is added to the gap around the part, and finally, the separating layer is removed by dissolution or etching to separate the micro part from the substrate.
1.7 Epitaxy Technology
Epitaxial growth is one of the important means of micromachining, it is characterized by the growth of epitaxial layer can maintain the same crystal direction with the substrate, and therefore in the epitaxial layer can be a variety of transverse and longitudinal doping distribution and etching process, in order to produce a variety of structures.
1.8 LIGA and quasi-LIGA technologies
(1 ) LIGA technology
LIGA technology was first developed by the German Research Center for Nuclear Physics in Karlsruhe and is recognized as a new three-dimensional microfabrication technology. The most important step is the production of high-precision mask, the most important step is the use of synchrotron radiation source for lithography, synchrotron radiation source generated by electron magnetic gas pedal, wavelength of 0.2 ~ 0.6nm, can produce high energy density and high parallelism of the ray.
Due to the deep penetration capability of X-rays, X-ray lithography can produce micromachines up to 1 mm in height with peripheral dimensions in the micron or submicron range, a size range that can only be achieved with the high energy of synchrotron radiation sources.
In order to create structures with cantilevers, sacrificial layer LIGA technology was developed. The sacrificial layer LIGA technology is an important micromechanical method for fabricating microdrivers and microsensors, and for creating microstructures with cantilevers and connecting microelectronic circuits.
The limitations of LIGA technology are the need for synchrotron X-ray light source, long processing time, complicated process, high price, and difficulty in fabricating microstructures with curved surfaces.
(2) Quasi-LIGA technology
LIGA technology has some unique advantages such as wide range of processed materials and high precision, but also has some of the above-mentioned drawbacks. In order to overcome LIG-
A process technology defects, the international research of quasi-LIGA technology, such as silicon quasi-LIGA technology, UV deep lithography, UV stereolithography, laser LIGA technology, etc..
①Si quasi-LIGA technology. Deep etching process is used instead of synchrotron X-ray deep lithography, followed by subsequent microelectroforming and
Microcopy process, which does not require expensive synchrotron light sources and special LIGA mask plates. After inductively coupled plasma (ICD: induc-tively coupled plasma) etching equipment for high aspect ratio plastic or silicon etching, microelectric casting is performed directly from the silicon wafer to obtain a metal mold, and then microcopy process is performed to achieve mass production of micromechanical devices. This technology allows for the fabrication of microstructures with high aspect ratios for non-silicon materials and better compatibility with microelectronic technology. The silicon quasi-LIGA technology can process thicknesses up to several hundred microns, with a sidewall perpendicularity of 90°±0.3° and an etching rate of more than 20 μm/min. This system is characterized by the use of SF6 as the main etching gas and does not require post-treatment processes. This high aspect ratio etching technology has advanced the application of silicon micromechanical process a great step forward and realized the high aspect ratio mold structure that could only be manufactured by LIGA technology in the past.
②Laser LIGA technology. Excimer laser with 193nm wavelength is used to directly ablate PMMA photoresist to replace X-ray lithography process. Since the excimer laser needs to replace the working gas regularly, the gas consumption is high and requires frequent maintenance, which also affects the production process. The YAG solid-state laser can work for a long time, and the lithography quality is more stable and reliable.
1.9 Special microfabrication technology
(1) Micro EDM
The principle of micro EDM is not fundamentally different from that of ordinary EDM. The key to realize micro EDM is the fabrication of micro axis (tool electrode), micro energy discharge power supply, micro servo feed of tool electrode, machining status detection, system control and machining process method. Since micro electrodes are extremely difficult or impossible to produce, it is not practical to use the traditional EDM method for micro 3D contour machining. With the application of micro EDM technology, micro axis of 2.5μm in diameter and micro hole of 5μm in diameter can be machined, and micro car molds of 0.5 mm in length, 0.2 mm in width and 0.2 mm in depth can be made, and micro car models have been made with them. Micro gears with a diameter of 0.3 mm and a module of 0.1 mm can be produced.
(2) Micro-fine electrolytic processing
Electrolytic processing is a manufacturing technology that uses the principle of electrochemical dissolution of the metal anode to remove material in the form of ionic dissolution. One of the major factors limiting the accuracy of electrolytic processing is the large processing gap. If the processing gap can be significantly reduced, the processing accuracy will be significantly improved and the possibility of microfabrication by electrolysis will be increased. By reducing the processing voltage and electrolyte concentration, the machining gap has been successfully controlled to less than 10μm. By using micro feed and metal micro tube electrode, the machining gap of 0.2mm NiA small hole of 0.17mm was machined in the plate.
Electrolytic machining is also used in the finishing of micro-shaft parts. In a method similar to EDM grinding of micro wire electrodes, a moving metal wire is used as the cathode and an electrolyte is sprayed between the anode shaft and the cathode wire to produce electrochemical microcorrosion on the shaft surface. This method has achieved good process results in polishing small shafts of tens of microns in diameter.
The size range involved in electrolytic microfabrication is much larger than the tiny sizes that can be achieved by silicon microfabrication and LIGA technology.
(3) Microfine ultrasonic processing
With the widespread use of hard and brittle materials such as crystalline silicon, optical glass and engineering ceramics in micromechanics, high-precision three-dimensional microfabrication technology for hard and brittle materials has become an important research topic. At present, the methods available for processing hard and brittle materials mainly include lithography, EDM, electrolysis, laser processing and ultrasonic processing. Compared with EDM, electrolysis and laser processing, ultrasonic processing does not depend on the electrical conductivity of the material and has no thermophysical effect; compared with photolithography, it can process a high depth to width ratio of three-dimensional structure, which determines the advantages of ultrasonic processing in the processing of non-metallic hard and brittle materials such as ceramics and semiconductor silicon.
Momentum.
Micro ultrasonic processing has the same principles and characteristics as conventional ultrasonic processing, except for the small size of the process. Since the amplitude required for conventional ultrasonic processing is generally between 0.01 and 0.1 mm, and the deformation of piezoelectricity or magnetostriction is very small (0.005 to 0.01 mm), the amplitude must be expanded by a thick upper and thin lower amplitude rod. The amplitude of piezoelectricity or magnetostriction can meet the requirements of microfabrication, so there is no need for a variable amplitude rod.
Using ultrasonic microfabrication technology, we have processed micropores with a minimum diameter of 5 μm on engineering ceramic materials by using workpiece vibration.
(4) Micro-fine laser forming process
Unlike traditional special processing methods, laser forming is not about removing material, but about adding material to achieve forming. Depending on the processing material and mechanism, laser forming can be divided into various types, such as light-curing forming, selective laser sintering forming, and layered solid modeling.
Light-curing molding is based on liquid photosensitive resin as raw material, and a far-ultraviolet light source is focused and irradiated on the surface of the liquid resin, and the exposed area is cured. Microstructures in the range of 10 μm to 1 mm can be obtained by light-curing molding. To solve the problem of mass production, precision fiber arrays can be used, and a large number of microstructures can be produced at one time:
① Depth accuracy is limited by the thickness of the layer laid; ② Influenced by the size effect (liquid photosensitive resin viscosity, surface tension); ③ Influence of microstructure deformation, etc.
forTo eliminate these effects, a new method of laser forming has emerged.
A focused laser beam is scanned in three dimensions in a resin tank, and the resin is cured only when the exposure threshold is exceeded at the focal point, enabling the creation of freely movable microstructures. The advantages of this technique are:
①Depth and peripheral accuracy are determined by the size of the laser focus point, and the accuracy is higher than 1μm in three-dimensional space; ②No support parts and no mask are required; ③The effect of resin viscosity and surface tension is eliminated because there are no moving parts in the liquid photosensitive resin tank.
(5) Precision electroforming
Electroforming hole making is different from cutting method, first of all, it is required to make the core of the hole, then the electroformed metal grows around it, and finally the core is withdrawn or dissolved. For the occasions that cannot be achieved by traditional removal processing, such as very fine holes and the workpiece with high internal surface roughness requirements or workpiece with special cross-sectional shape, electroforming can be used.
Most of the core materials are aluminum alloys, which dissolve in sodium hydroxide solution, but nickel is not damaged and can work safely. When it is difficult to cut aluminum cores that are particularly fine, brass can be used to make the cores instead.
No matter what shape of the hole, its dimensional accuracy and surface roughness are determined by the quality of the core, so no matter how fine the hole, as long as you can use a certain processing method to create the core, you can use electroforming method to process the hole.
We offer fastMEMS device / micro and nanostructure processing design services, Feel free to leave a message to inquire.
Related Products
Related Reading
Micro and Nano Processing | For Cellular Arraying
Micro and Nano Processing | for Cellular Arraying Cellular Microarraying (or
MEMS Foundry Capabilities | Photolithography Plating Etching Coating
Micro and nano structure/MEMS foundry platform technology capability Laboratory platform has
Micro and Nano Processing | Etching
Micro and Nano Processing | Etching Once the resist film is patterned by photolithography