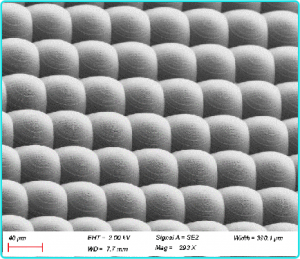
Micro and Nano Processing | Electron Beam Lithography Principles
The advantage of electron beam lithography over the available optical techniques is the ability to manufacture components with smaller feature sizes. The feature size of a component is essentially limited by the wavelength of the light wave used. The spot size of the electron beam used in electron beam lithography can range from a few nanometers to several hundred nanometers depending on the application. The deBroglie wavelength of an electron is
where Vb is the acceleration voltage. Most electron beam systems operate at voltages above 1 kV, and the electron wavelength in electron beam lithography has no effect on the resolution that can be achieved.
Electron beam lithography systems are widely used for the fabrication of photolithography masks, advanced principle prototypes, and nanoscale scientific research and development. State-of-the-art electron beam lithography systems can transfer graphics (by metal stripping, etching or color addition techniques) at extreme sizes of less than 10 nm at ultra-high resolution. In addition, such patterns can be processed on a variety of materials, such as semiconductors like Si and GaAs, fused silica, amorphous diamond, insulators like SiO2 and SiN, and various metals.
Ordinary electron beam lithography is the deterministic scanning of electron-sensitive resist surfaces by a highly focused electron beam. Electron beam lithography can use a variety of positive and negative resists. In high-resolution lithography systems, a hot-field emission source is often used, such as a beam of electrons formed with a ZrO/W emitter. Several stages of electrostatic and/or magnetic lenses focus the electron beam and shape it within the electron gun, using electromagnetic deflection coils to scan the beam over an effective field of view (typical values of 0.1 to 1 mm on one side, depending on the system and electron beam parameters). Dedicated electron beam lithography systems are generally used with the aid of a laser interferometric table in order to move the sample during exposure in different working fields of view. When the interferometric table is moved, the interference fringes are calculated so that the splicing error or offset error between adjacent beam writing ranges can be minimized (less than 20 nm). A set of electrostatic beam shields is also used to deflect the electron beam out of the optical path of the electrons when needed.
A computer system is used to control the deflection coil, thus enabling graphic inscription and mask control, and ultimately the amount of electron exposure incident to a specific square hole is adjusted. The area exposure formula can be simply written as
Dose × area = electron beam current × residence time = total number of incident electrons
As can be seen by increasing or decreasing the exposure, exposure time and electron beam current values, the biggest disadvantage of electron beam lithography is that the series exposure process results in longer etching times. With a high resolution beam current of about 500 pA, assuming a 300 nm thick 495 K polymethyl methacrylate (PMMA) (about 1000 μC/cm2 for a 50 kV accelerating voltage divider), a 25 MHz graphic generator, and a hole size of 10 nm, it takes about 5.5 h to etch an area of 1 cm2 (50% coverage area). Once you add the movement time of the interferometer and the "dwell" time of the electron beam, i.e., the waiting time for the beam to stabilize between deflections, it is clear that inscribing a large area will be particularly time-consuming.
The use of alignment marks allows the electron beam lithography pattern to be aligned with existing features on the sample. These marks can be painted out or etched out, and are typically simple geometric shapes or crosses. They must be imaged by backscattering electrons at high contrast, and so are usually composed of metal (e.g., gold) or etched surface structures. The operator then proceeds to prepare job files that identify and use existing marks on the substrate surface to determine and compensate for rotation, gain, and position errors.
We offer fastMEMS device / micro and nanostructure processing design services, Feel free to leave a message to inquire.
Related Products
Related Reading
MEMS Foundry Capabilities | Photolithography Plating Etching Coating
Micro and nano structure/MEMS foundry platform technology capability Laboratory platform has
Micro and Nano Processing | MEMS Fine Processing (VII)
Micro and Nano Processing | MEMS Fine Processing (VII) 1.10 Key
Micro and Nano Processing | E-paper micro-cups and micro-chamber structure preparation
Microfabrication | E-paper microcups microchamber type structure preparation For when